Are you trying to pick the right HPMC grade for your product? Many buyers get confused when choosing between HPMC E15 and other grades. This can lead to failed products and costly do-overs. The wrong choice often causes delays, poor results, and rule problems. This guide shows how HPMC E15 compares to other grades. You’ll learn how to make smart choices based on what your product needs. Tests show that picking the right HPMC grade can cut your work time by 30%. We’ll look at what makes HPMC E15 special, how it differs from other grades, and how to pick the best one for your needs.
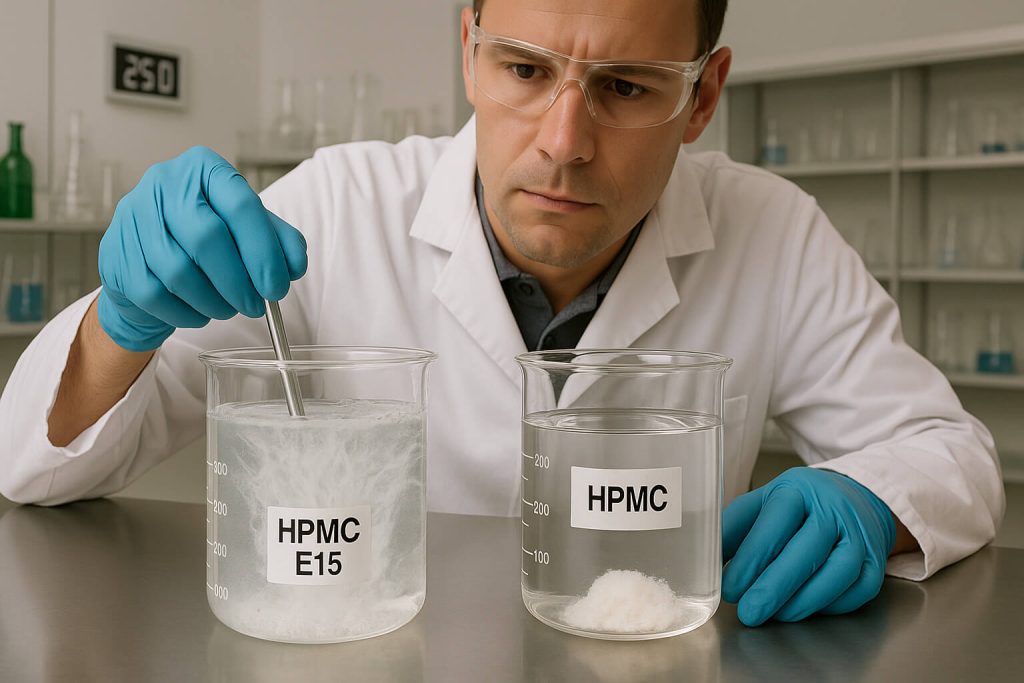
1. What Are The Key Properties Of HPMC E15?
HPMC E15 stands out from other grades because of its unique traits. The “E” means ethoxy content. The “15” shows its thickness when mixed at 2% in water at 20°C. This grade offers a middle-range thickness that works well for many uses.
The makeup of HPMC E15 has a cellulose base with methoxy and hydroxypropyl groups attached. These groups give E15 its special traits. But here’s what matters most: the methoxy content runs from 28-30%. The hydroxypropyl content ranges from 7-12%. This pattern affects how the polymer acts in different settings.
When we look at the thickness profile, E15 responds in a steady way when you change how much you use. A 2% mix gives about 15 mPa·s thickness at 20°C. This makes it easier to work with than thicker grades that might cause mixing problems.
Property | HPMC E15 Value | Why It Matters |
---|---|---|
Viscosity (2% solution) | 15 mPa·s | Controls flow and ease of use |
Methoxy Content | 28-30% | Affects water mixing and heat gelling |
Hydroxypropyl Content | 7-12% | Changes how it mixes with organic solvents |
Molecular Weight | 22,000-26,000 Da | Affects film strength and sticking power |
Particle Size | 100-150 μm | Changes how fast it dissolves and spreads |
The weight of HPMC E15 centers around 22,000-26,000 Daltons. This range gives good film-forming without being too thick. HPMC E15 looks like a white to off-white powder that flows well. The particle size usually ranges from 100-150 microns. This helps it dissolve at a medium rate without too much dust when handling.
You can spot HPMC E15 by its free-flowing nature and medium particle size. When you add it to cold water, it forms a clear solution after proper mixing. This clarity helps in many uses where the final product needs to look good. The powder also has no smell or taste. This makes it perfect for food and drug uses.
Many users find that HPMC E15 mixes more easily than higher grades. You don’t need special high-power mixers like you might with E4M or higher grades. A simple mixer often works fine for E15 solutions up to 5% strength. This saves time and equipment costs for many companies.
2. How Does HPMC E15 Compare To E5 And E50 Grades?
When we compare HPMC E15 with E5 and E50 grades, the main difference is in their thickness levels. E5 has a much lower thickness (5 mPa·s in a 2% mix). E50 has a much higher thickness (50 mPa·s in a 2% mix). You might wonder why this matters so much. The thickness directly affects how the polymer works in your product.
E15 hits a sweet spot between the easy-flowing E5 and the thickening power of E50. This middle position makes it useful for many tasks. For pill coatings, E15 makes films that aren’t too thin (like E5 might make) or too thick and hard to spray (like E50).
HPMC Grade | Viscosity (mPa·s) | How Fast It Dissolves | Film Thickness | Ease of Use |
---|---|---|---|---|
E5 | 5 | Fast | Thin | Very Easy |
E15 | 15 | Medium | Medium | Medium |
E50 | 50 | Slow | Thick | More Difficult |
E4M | 4,000 | Very Slow | Very Thick | Hard |
E10M | 10,000 | Extremely Slow | Extremely Thick | Very Hard |
The dissolving speed also varies a lot between these grades. E5 dissolves quickly but may not be thick enough for many uses. E50 dissolves more slowly and needs careful mixing. E15 offers a practical middle ground with good dissolving speed and enough thickness.
Heat effects vary between these grades too. All HPMC grades form gels when heated. The gel point and how sharply they change differ. E15 typically gels around 65-70°C. E5 might need slightly higher temps. E50 might need slightly lower ones.
A drug company switched from E50 to E15 for their pill coating. They saved 15% on material costs while keeping product quality high. Food makers often prefer E5 for clear mixes with minimal texture change. Building material makers might choose E50 for its stronger water holding power.
The surface tension of solutions also differs between grades. E15 solutions show medium surface tension reduction. This helps with wetting and spreading in coating uses. E5 has less effect on surface tension. E50 and higher grades can reduce surface tension more strongly. This affects how the solution spreads on surfaces during use.
Film flex also varies among grades. E15 films have medium flex. They’re not as bendy as E5 films but more bendy than E50 films. This matters for coating uses where the film needs to bend without cracking. Tablet coatings made with E15 resist cracking better during handling than those made with E50.
3. What Manufacturing Processes Affect HPMC E15 Performance?
The making of HPMC E15 greatly impacts its final traits. Production starts with pure cellulose. It gets treated with sodium hydroxide to create alkali cellulose. What’s fascinating is this treated cellulose then reacts with methyl chloride and propylene oxide. This adds the methoxy and hydroxypropyl groups that define HPMC E15.
Quality checks throughout production ensure steady patterns. Makers carefully watch reaction conditions. These include heat, pressure, and reagent ratios. Even small changes can alter the final product’s traits.
Manufacturing Factor | Impact on HPMC E15 | Quality Check Method |
---|---|---|
Cellulose Source | Affects purity and reactivity | Supplier testing |
Alkalization Conditions | Sets reactivity pattern | Process monitoring |
Reagent Ratio | Controls substitution degree | Sample testing |
Washing Efficiency | Removes by-products | Conductivity testing |
Drying Parameters | Affects particle size and moisture | Moisture testing |
Particle size greatly affects how HPMC E15 performs in uses. Smaller particles dissolve faster but may cause dust issues when handling. Larger particles flow better but take longer to wet fully. Most makers aim for a size around 100-150 microns for E15 grade.
Batch consistency factors include tight control of all process steps. Leading makers use statistical process control methods. These help catch and fix problems before they affect the final product. A case study from a major HPMC producer showed good results. Using advanced process controls cut batch-to-batch thickness variation from ±15% to less than ±5%.
The drying method used after washing also affects the final product quality. Flash drying creates more porous particles. These dissolve faster but may have lower bulk density. Fluid bed drying tends to make denser particles with more uniform size. The choice of drying method affects how HPMC E15 behaves in your process.
Milling operations after drying can fine-tune the particle size. Too much milling can create too many fines. These cause dusting and clumping issues. Too little milling might leave large particles. These dissolve slowly. The best HPMC E15 products have a carefully controlled milling step. This optimizes particle size for good flow and fast dissolving.
Storage during making also matters. HPMC E15 can absorb moisture from humid air. This affects its flow and dissolving rate. Good makers store the product in controlled humidity rooms. They use moisture-proof packaging. This maintains quality until it reaches your facility.
4. Which Industries Benefit Most From HPMC E15?
The drug industry gains the most from HPMC E15’s unique traits. Drug makers value this grade for its steady performance in controlled-release matrix tablets. The key advantage here is that E15 provides predictable drug release rates. It lacks the excessive thickness that makes higher grades hard to process. A major generic drug maker reported 30% faster tablet production when using E15 compared to thicker grades.
In tablet coating, E15 creates films with excellent evenness and sticking power. The medium thickness allows for easy spraying. It provides enough film thickness in a single pass. This balance cuts coating time and energy use.
Industry | HPMC E15 Use | Main Benefit | Typical Amount Used |
---|---|---|---|
Pharmaceutical | Controlled-release matrices | Predictable drug release | 20-30% of tablet weight |
Pharmaceutical | Film coating | Even coverage, good processing | 6-8% in coating solution |
Construction | Tile adhesives | Water holding without too much stiffening | 0.2-0.4% of dry mix |
Construction | Renders and plasters | Better workability and sag resistance | 0.1-0.3% of dry mix |
Food | Bakery products | Moisture holding without gumminess | 0.1-0.2% of flour weight |
Building material mixes benefit from HPMC E15’s water holding traits. In tile glues, mortars, and plasters, E15 helps maintain workability. It doesn’t make the mix too stiff or hard to apply. The medium thickness improves sag resistance on walls. It doesn’t need too much mixing effort.
Food product uses leverage HPMC E15 for texture change and moisture holding. Baked goods with E15 stay fresh longer. They don’t have the gummy texture that thicker grades might create. The heat gelling trait also helps maintain structure during baking.
Personal care product makers choose E15 when they need medium thickening and film-forming traits. In shampoos and body washes, it provides just enough thickness. The product isn’t too thick and hard to pour out.
The printing ink industry also uses HPMC E15 as a thickener and binder. Water-based inks with E15 show good flow during printing. They dry quickly after use. The medium thickness helps control ink spread on paper or other surfaces. Ink makers report better color density and less bleeding when using E15 compared to lower viscosity grades.
Farm product makers use HPMC E15 in seed coatings and crop protection products. The polymer helps stick active parts to seeds or plant surfaces. It also controls the release rate of nutrients or pesticides. Farmers get better results. The active parts stay where needed longer. The medium viscosity of E15 makes spray use easier than with higher grades.
5. How Does Temperature Affect HPMC E15 Behavior?
Heat strongly influences how HPMC E15 acts in solution. One of its most unique traits is heat gelling. It forms a gel when the solution heats above a certain point. What you’ll find surprising is that this behavior is opposite to most polymers. Most become more mixable at higher temps. For E15, the gelling point typically falls between 65-70°C.
This reverse mixing happens because heating disrupts the water molecules around the polymer chains. At lower temps, water molecules form hydrogen bonds with the hydroxyl groups on HPMC. As heat rises, these bonds weaken. This allows polymer-polymer links to take over. Then gel formation occurs.
Temperature Range (°C) | HPMC E15 Behavior | Application Tip |
---|---|---|
5-20 | Slow dissolving, higher final thickness | Allow longer mixing time in cold |
20-50 | Good dissolving, medium thickness | Ideal range for most uses |
50-65 | Decreasing thickness, nearing gel point | Watch carefully during heated processing |
65-70 | Rapid thickness increase, gel formation begins | Avoid this range during liquid processing |
>70 | Strong gel formation | Can be used for heat structuring in some uses |
Stability in various conditions depends on both heat and other factors. In dry form, HPMC E15 stays stable at temps up to 200°C for short periods. This makes it good for hot-melt extrusion. In solution, however, long exposure to temps above 50°C may cause gradual breakdown through hydrolysis.
Processing temperature tips vary by use. For initial mixing and dissolving, use cold water (below 20°C). This prevents immediate hydration. It allows better particle spreading. Once fully mixed, the solution can be warmed to 30-40°C. This reduces thickness during processing steps like spraying or mixing.
The cooling rate after heating above the gel point also affects HPMC E15 behavior. Fast cooling can trap the gel structure. This creates a firmer texture. Slow cooling allows more time for the polymer chains to reorganize. This often results in a softer gel. Food makers use this property to control texture in products like veggie meat substitutes.
Freeze-thaw stability presents another temperature factor. HPMC E15 solutions show good stability through multiple freeze-thaw cycles. The polymer helps prevent ice crystal growth. This can damage product structure. This makes E15 useful in frozen food uses where texture matters.
Temperature cycling during storage can affect dry HPMC E15 powder. Cycling between warm days and cool nights can cause moisture movement within packaging. This leads to clumping. The best storage conditions maintain steady temperature and low humidity. Many users find that climate-controlled warehousing extends the shelf life. It maintains free-flowing properties.
6. What Are The Compatibility Factors With Other Ingredients?
HPMC E15 interactions with active drug parts (APIs) can greatly impact drug product performance. Most APIs stay stable when mixed with HPMC E15. There are exceptions. You should know that positively charged drug molecules may bind to the slightly negative HPMC polymer. This can change dissolution profiles. For example, a study with metoprolol tartrate showed an effect. Drug-polymer interaction reduced initial release rates by about 15% compared to theory.
Compatibility with other polymers and excipients generally stays good. This makes HPMC E15 versatile in complex formulations. It works well alongside other cellulose derivatives. These include microcrystalline cellulose or ethylcellulose.
Ingredient Type | Compatibility with HPMC E15 | Notes |
---|---|---|
Basic APIs (pH >7) | Good to Excellent | Minimal interaction in most cases |
Acidic APIs (pH <7) | Good | Watch for potential thickness changes |
Cationic APIs | Fair | May bind to polymer, affecting release |
Other cellulose derivatives | Excellent | Often used together for better traits |
Polyvinyl alcohol | Good | Creates complementary film traits |
Multivalent metal ions | Poor to Fair | Can cross-link and cause precipitation |
Surfactants | Good to Excellent | Often improves HPMC dissolving |
pH sensitivity plays an important role in HPMC E15 performance. The polymer maintains relatively stable thickness between pH 3-11. This makes it suitable for most drug and food uses. Below pH 3, acid hydrolysis may gradually reduce molecular weight and thickness during long storage.
Buffer systems can help maintain optimal conditions for HPMC E15 performance. Phosphate buffers at pH 6-8 work particularly well with HPMC in drug uses. Citrate buffers also show good compatibility. They may slightly reduce solution thickness at equal concentrations.
Antioxidants often work well with HPMC E15 in formulations exposed to air or light. The polymer itself resists oxidation. It can help protect other parts that might degrade. Adding small amounts of antioxidants like BHT or ascorbic acid can extend shelf life. This won’t affect HPMC performance.
Preservatives mix well with HPMC E15 in water-based formulations. The polymer doesn’t support microbial growth. It can provide a hospitable environment for microbes if contaminated. Common preservatives work effectively in HPMC solutions without compatibility issues. These include parabens, benzalkonium chloride, or potassium sorbate.
Colorants and pigments can be added into HPMC E15 formulations with good results. The polymer helps suspend insoluble pigments. It prevents settling. This makes it useful in colored coatings and inks. The medium viscosity of E15 provides good pigment suspension. It’s not too thick to process.
7. How Should You Select Between HPMC E15 And Alternatives?
Choosing between HPMC E15 and other grades requires a structured decision approach. Start by defining your critical quality needs. What traits must your final product have? This approach works wonders: rank these traits by importance. Then match them against the traits of different HPMC grades. For controlled-release tablets, drug release rate might be most critical.
A step-by-step selection process begins with screening tests. Use small samples of different grades. Test the most critical traits first to narrow down options quickly. A drug formulator tested three HPMC grades for a controlled-release product. E15 provided the target 12-hour release profile. E5 released too quickly (8 hours). E50 released too slowly (16+ hours).
Selection Factor | HPMC E5 | HPMC E15 | HPMC E50 | HPMC K15M |
---|---|---|---|---|
Viscosity (2% solution) | 5 mPa·s | 15 mPa·s | 50 mPa·s | 15,000 mPa·s |
Dissolution Speed | Very Fast | Medium | Slow | Very Slow |
Processing Ease | Excellent | Good | Medium | Hard |
Film Strength | Low | Medium | High | Very High |
Cost Per Kg (Relative) | 0.8x | 1.0x | 1.2x | 1.8x |
Typical Amount Needed | Higher | Medium | Lower | Much Lower |
Cost-benefit analysis should account for both direct material costs and process implications. Higher thickness grades like E50 cost more per kilogram than E15. You might use less material to achieve the same effect. However, also consider processing costs. Higher thickness solutions need more energy to mix and pump.
Performance testing should evaluate use-specific traits. For drug coatings, test film formation, adhesion strength, and dissolution profile. For building products, assess water retention, sag resistance, and open time.
Regulatory considerations vary by region and use. Drug uses must meet pharmacopeia standards (USP, Ph.Eur., JP) for the specific HPMC type. Food uses require proper food additive clearances. These may differ between regions.
Pilot scale testing provides crucial insights before full production. Small lab tests might not reveal processing issues that appear at larger scales. Many companies run pilot batches with different HPMC grades. They compare real-world performance. This step often reveals handling, mixing, or application differences not seen in small tests.
Supply chain reliability should factor into your decision. Some HPMC grades have more suppliers than others. This affects availability and price stability. E15 has good availability from multiple global suppliers. This reduces supply risk. Less common grades might have limited sources. This creates potential supply chain risks.
Long-term stability testing helps predict how your product will perform over its shelf life. Different HPMC grades can affect stability differently. A six-month accelerated stability study can reveal which grade provides the best long-term performance for your specific product. Compare formulations with E5, E15, and E50.
Conclusion
HPMC E15 offers a balanced profile that sets it apart from other HPMC grades. It has medium thickness, optimal dissolving rate, and versatile use potential. This article has outlined the key traits, industry uses, temperature behaviors, and compatibility factors that make E15 unique. By understanding these differences, you can make smarter choices for your specific formulation needs. Companies using the right HPMC grade have reported up to 25% improvement in manufacturing efficiency and product performance. Contact Morton today to request samples of our pharmaceutical-grade HPMC E15 for your testing. Our technical team can provide custom recommendations based on your specific use requirements to help you achieve optimal results.
FAQ
Q1: Can HPMC E15 be directly substituted for other HPMC grades?
Direct substitution depends on your use requirements. While E15 can replace E5 or E50 in many cases, you may need to adjust amount. For E5 replacement, you’ll typically use 60-70% of the original amount of E15. When replacing E50, you’ll need about 130-150% more E15. Always conduct small-scale tests before full production changes.
Q2: What testing methods verify HPMC E15 quality?
Standard testing methods include thickness measurement of a 2% solution at 20°C using a rotational viscometer. Other tests check methoxy and hydroxypropyl content through gas chromatography. Moisture content is tested via loss on drying. Particle size distribution uses laser diffraction or sieve analysis. USP and Ph.Eur. monographs provide detailed testing protocols.
Q3: How does HPMC E15 affect drug release profiles?
HPMC E15 creates a hydrated gel layer around tablets that controls drug diffusion. The medium thickness of E15 typically produces medium release rates. These are slower than E5 but faster than E50 or K-series grades. Drug solubility, tablet makeup, and manufacturing method also affect the final release profile. E15 works best for drugs requiring release over 8-12 hours.
Q4: What are the environmental impacts of HPMC E15 production?
HPMC E15 production has a medium environmental footprint. The raw material (cellulose) comes from renewable sources. This is typically wood pulp from managed forests. The manufacturing process uses propylene oxide and methyl chloride. These require careful handling. Modern production facilities use closed-loop systems. These capture and reuse solvents, minimizing emissions.
Q5: How do storage conditions affect HPMC E15 stability?
HPMC E15 powder stays stable for 3+ years when stored in sealed containers in cool, dry conditions. These should be below 30°C and 60% relative humidity. High humidity can cause partial hydration and clumping. Temperature cycling may lead to moisture migration and caking. Once in solution, HPMC E15 should be used within 48-72 hours at room temperature. This avoids microbial growth, unless preservatives are added.