Picking the right HPMC thickness grade matters a lot. Many firms pick grades out of habit, not based on real needs. This leads to making problems, poor quality, and waste. Wrong HPMC thickness can cause poor water holding in building mixes, uneven drug release in pills, or unstable food. Good news! When you know how thickness works and what you need, you can make better products for less money. Firms that pick the right HPMC grade can cut costs by up to 15%. They also make better products. This guide will help you learn HPMC basics, know the grades, and make the best choice.
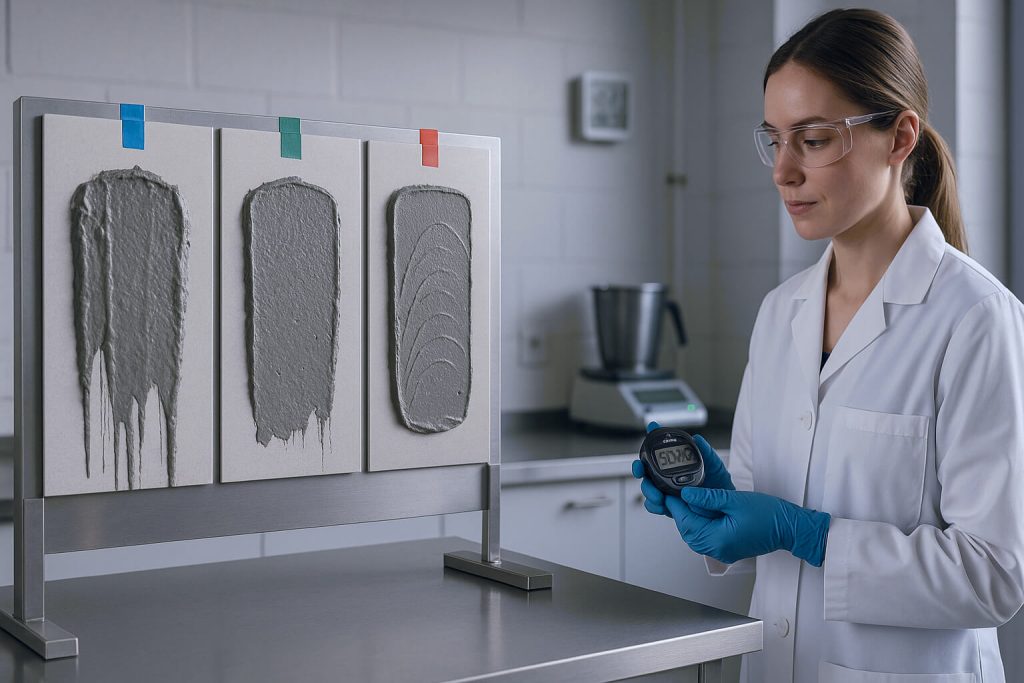
1. What Is HPMC and Why Does Its Viscosity Matter?
HPMC is a plant-based stuff used in many products. It works in building mixes, pills, and foods.
Here’s what makes it special: HPMC’s thickness affects how your products work. When mixed with water, HPMC forms a gel. This gel controls water holding, binding, and how things release.
HPMC thickness depends on:
- Size of the bits
- Chemical makeup
- Amount used
- Heat
- Mixing force
Factor | Effect on Thickness | Impact on Use |
---|---|---|
Bit Size | Bigger = Thicker | Affects cost and amount needed |
Chemical Makeup | Changes water mixing | Affects how it works at different heats |
Amount Used | More = Much thicker | Sets how much you need |
Heat | Complex effects | Affects mixing and stability |
In building mixes, HPMC thickness controls water holding in mortars and glues. This affects working time and bond strength. A tile glue with too low thickness might dry too fast. This gives workers less time to place tiles.
In pills, HPMC thickness controls how fast drugs release. Higher thickness makes thicker gel layers around pills. This slows drug release for time-release pills.
Food makers use HPMC to create stable mixes and better texture. The wrong thickness can cause food to split or feel bad.
The bottom line? Choosing wrong wastes money and hurts quality. One building mix maker switched from a thicker to a thinner HPMC grade. They saved 12% on stuff while keeping the same water holding. This shows how the right choice saves money and keeps quality.
2. What Are the Different Viscosity Grades of HPMC Available?
HPMC comes in many thickness grades for different uses. Makers group these grades based on the thickness of a 2% water mix at 20°C.
HPMC thickness is measured in mPa·s or cP, with 1 mPa·s equal to 1 cP. Most sellers use names that show both the chemical type and thickness.
Thickness Group | Range (mPa·s) | Common Uses |
---|---|---|
Very Low | 3-10 | Pill coatings, sprays |
Low | 10-100 | Cement adds, paint thickeners |
Medium | 100-4,000 | Tile glues, pill binders |
High | 4,000-15,000 | Time-release pills, wall coatings |
Very High | 15,000-100,000+ | Special building mixes, long-release pills |
Low thickness HPMC (10-100 mPa·s) mixes well in water. It works where you need just a bit of thickening. These grades melt fast and flow well. They’re used in:
- Cement mixes to hold water
- Pill binding where little gel strength is needed
- Paint as helpers
- Paper and cloth making
You should know that low thickness grades often cost less per pound than higher thickness types. But you might need to use more to get the same effect. This can offset the price edge.
Medium thickness HPMC (100-4,000 mPa·s) balances thickening power and clarity. These handy grades work in:
- Tile glues and self-leveling floors
- Pill making
- Food thickeners
- Shampoos and lotions
High thickness HPMC (4,000-15,000 mPa·s) makes strong gels and holds water well. They’re great for:
- Outer wall systems
- Slow-release pills
- Products needing strong binding
- High water holding needs
Very high thickness grades (15,000-100,000+ mPa·s) give max thickening with small amounts. These top grades work in:
- Special building mixes needing extreme water holding
- Very slow-acting pills
- Uses where you need to use very little
Grade Example | Thickness (mPa·s) | Typical Uses |
---|---|---|
HPMC E5 | 5 | Pill coating, cement changing |
HPMC E15 | 15 | Building mixes, binding |
HPMC K100M | 100,000 | Slow release pills, special mortars |
HPMC F4M | 4,000 | Controlled release, wall coatings |
HPMC E4M | 4,000 | Basic thickener |
When picking grades, know that higher thickness grades:
- Need less for the same water holding
- Make stronger gels
- Melt more slowly
- Cost more
- May change workability
3. How Does HPMC Viscosity Impact Construction Applications?
In building mixes, HPMC thickness affects water holding, workability, sag fighting, and open time. These traits set how easily workers can use mixes and how well they work once set.
Water holding is maybe the most key job of HPMC in building mixes. When cement mixes with water, chemical changes start right away. Without good water holding, these changes can happen too fast. This is worse in hot or windy weather.
What you need to know is higher thickness HPMC grades often hold water better. This link isn’t always straight, though. A test of many HPMC grades in cement mortars showed that a 15,000 mPa·s grade at 0.3% gave like water holding to a 100,000 mPa·s grade at 0.2%.
HPMC Thickness Grade | Typical Amount in Mortars | Water Holding | Open Time | Workability Impact |
---|---|---|---|---|
5-15 mPa·s | 0.5-0.8% | Low | Short | Little thickening |
100-400 mPa·s | 0.3-0.5% | Medium | Medium | Even traits |
4,000-15,000 mPa·s | 0.2-0.4% | High | Long | Big thickening |
30,000-100,000 mPa·s | 0.1-0.3% | Very High | Extra Long | May cut flow |
Workability and open time go with water holding. Open time means how long the mix stays workable after use. For tile glues, longer open time gives workers more time to fix tile spots.
A tile glue maker tested different HPMC thickness grades and found:
- Low thickness (50 mPa·s): 10 minutes open time, poor sag fighting
- Medium thickness (4,000 mPa·s): 20 minutes open time, good sag fighting
- High thickness (15,000 mPa·s): 30 minutes open time, great sag fighting
Sag fighting matters most in wall uses like tile setting or coatings. Higher thickness HPMC grades help sag fighting. They make stronger gels that hold mixes in place against gravity.
Use | Best HPMC Thickness | Key Needs |
---|---|---|
Tile Glues | 4,000-15,000 mPa·s | Long open time, sag fighting |
Self-Leveling Floors | 100-4,000 mPa·s | Flow traits, medium water holding |
Wall Coatings | 15,000-50,000 mPa·s | High water holding, strong sag fighting |
Joint Mixes | 15,000-30,000 mPa·s | Workability, crack fighting |
Cement-Based Paints | 400-4,000 mPa·s | Spatter fighting, sticking |
Common mistakes in thickness picking for building mixes are:
- Using too high thickness for self-leveling floors, cutting flow
- Picking too low thickness for wall uses, causing sagging
- Not thinking of local weather when making mixes
- Missing how HPMC works with other adds
4. What Role Does HPMC Viscosity Play in Pharmaceutical Formulations?
In pills, HPMC thickness affects drug release rates, making steps, and the stability of pill types. The right thickness grade can mean the gap between a pill that works right and one that fails.
Drug release rates depend a lot on the thickness of the HPMC used in pills. When a pill with HPMC meets stomach fluids, it forms a gel layer. This gel controls drug flow.
What makes this key is higher thickness grades make thicker gel layers. These slow drug release. Lower thickness grades allow faster release. This link makes HPMC thickness picking a main tool for making time-release pills.
HPMC Thickness Grade | Gel Layer Making | Drug Release Rate | Typical Release Time |
---|---|---|---|
5-50 mPa·s | Thin, quick-forming | Fast | 1-4 hours |
100-4,000 mPa·s | Medium thickness | Medium | 4-8 hours |
4,000-15,000 mPa·s | Thick, strong | Slow | 8-12 hours |
15,000-100,000+ mPa·s | Very thick, very strong | Very slow | 12-24+ hours |
For fast-release pills, makers often pick low thickness grades (3-15 mPa·s). These work mainly as binders not release slowers. These grades help hold the pill together. They don’t much slow drug melting.
Slow-release pills use medium to very high thickness grades. A common way uses a mix of different thickness grades. This gets set release rates:
- First burst release: Low thickness part (50-100 mPa·s)
- Middle release phase: Medium thickness part (4,000 mPa·s)
- Long release phase: High thickness part (15,000-100,000 mPa·s)
Making steps are also changed by HPMC thickness. During pill making:
- Low thickness grades flow better in hoppers and die holes
- High thickness grades may need more pressing force
- Very high thickness grades might need special making tools
Pill Type | Best HPMC Thickness | Making Thoughts |
---|---|---|
Fast Release Pills | 3-15 mPa·s | Good flow, little pressing force |
Slow Release Pills | 4,000-100,000 mPa·s | May need higher pressing force |
Capsule Mixes | 3-100 mPa·s | Must flow into capsule shells |
Pill Coating | 3-15 mPa·s | Sprayability, film making |
Eye Drops | 4,000-15,000 mPa·s | Clean filtering needs |
5. How Should You Test and Measure HPMC Viscosity for Your Application?
Good thickness testing is key for picking the right HPMC grade. It also helps make sure your product works the same each time. There are many test ways. Each has its own uses and limits.
The most common test way uses a turning tool to measure the thickness of a 2% HPMC mix at 20°C. This basic way lets you match different grades and makers.
You should know that heat greatly changes HPMC thickness tests. A 5°C heat rise can cut measured thickness by 10-15%. This heat link makes set test states key for good results.
Test Way | Tool | Good Points | Limits | Best For |
---|---|---|---|---|
Turning Test | Brookfield Tool | Industry basic, can be redone | Single shear rate test | Quality checks, grade matching |
Tube Test | Ubbelohde Tool | Easy to run, good for low thickness | Only for low thickness ranges | Study, low thickness grades |
Flow Test | Rheometer | Tests across shear rates, gives flow curves | Hard to run, costly | R&D, deep study |
Falling Ball | Falling Ball Tool | Easy, can move | Limited truth | Field tests |
Cup Ways | Ford/Zahn Cup | Fast, handy | Only for low thickness ranges | Making floor checks |
When testing HPMC thickness, follow these steps:
- Make a 2% mix by putting HPMC in hot water (80-90°C)
- Cool the mix to 20°C with light stirring
- Let the mix stand for 12 hours for full water take-up
- Keep set heat control during test
- Use the right spinner and turn speed for your tool
- Take reads after the test settles (often 30-60 seconds)
6. What Factors Should Guide Your HPMC Viscosity Selection Process?
Picking the best HPMC thickness grade needs a step-by-step way. Look at many things past just the thickness number. This choice should mix use needs, making skills, money thoughts, and setting factors.
Start with a full look at your use’s set needs. Different uses want different HPMC traits:
The key point here is that thickness picking should be led by working needs not habit. Many makers keep using the same grade for years. They don’t check if it’s truly best for their now mixes.
Use Type | Main Working Needs | Other Thoughts | Thickness Range Guide |
---|---|---|---|
Cement-Based Mortars | Water holding, workability | Open time, sag fighting | 15,000-50,000 mPa·s |
Tile Glues | Open time, sag fighting | Fixing, wetting | 4,000-15,000 mPa·s |
Self-Leveling Mixes | Flow traits, fair water holding | Setting time, top finish | 100-4,000 mPa·s |
Slow Release Pills | Set drug release rate | Making ease | 4,000-100,000 mPa·s |
Fast Release Pills | Binding strength, breaking up | Flow traits, pressing | 3-15 mPa·s |
Food Thickeners | Feel, stability | Mouth feel, clarity | 4,000-15,000 mPa·s |
Making tool fit is one more key factor. Your making setup may limit your thickness choices:
- High-shear mixers can handle higher thickness grades
- Spray uses need lower thickness for good spraying
- Pill pressing tools may fight with very high thickness grades
- Pumping systems have max thickness limits
Money thoughts should balance raw stuff costs against working gains. Higher thickness grades often:
- Cost more per kilo
- Need lower amounts for same working
- May cut the need for other adds
- Can make end-product working and worth better
Conclusion
Picking the right HPMC thickness grade needs balancing tech needs, making skills, and money factors. In this guide, we’ve seen how thickness affects water holding in building mixes, drug release in pills, and stability in many uses. By knowing these links, you can make smart choices that make both working and cost better. Firms that master HPMC thickness picking often cut mix costs by 10-20%. They also make product quality better. For expert help on picking the perfect HPMC grade for your set use, call Morton’s tech team today. Our pros can study your needs and push the best thickness grade. This could save you thousands in mix costs while making your product working better.
FAQ
Q1: Can different viscosity grades of HPMC be mixed to achieve intermediate properties?
Yes, you can mix different HPMC thickness grades to get custom traits. This works well for tuning drug release in pills or changing water holding in building mixes. For best results, mix grades with like chemical patterns but different thickness. The end thickness won’t be a simple middle—it follows a log link. Always test the mixed system well. Sometimes grades can mix in ways you don’t expect.
Q2: How does temperature affect the viscosity behavior of HPMC solutions?
HPMC mixes show odd heat-based traits. At lower heats, thickness drops a bit as heat rises. This follows normal polymer ways. But when the mix hits its heat gel point (often 65-80°C based on grade), thickness jumps up. This happens as the polymer forms a gel net. This trait makes HPMC good in uses needing heat-set thickening. During making, keep heats below the gel point. This keeps workability.
Q3: What are the key differences between HPMC and other cellulose ethers in terms of viscosity performance?
HPMC differs from other cellulose ethers like MC, CMC, and HEC in many ways. Next to MC, HPMC has better melting in cold water and oil mixes. Unlike CMC, HPMC is non-ionic. This makes it less changed by salt and pH shifts. HEC lacks HPMC’s heat gel traits. HPMC often gives better water holding than HEC at same thickness. CMC often makes more stringy mixes than HPMC at the same thickness level.
Q4: How do storage conditions affect the viscosity stability of HPMC products?
Storage states greatly impact HPMC stability. High wet (>70% RH) can cause part water take-up. This leads to lumping and slower melting speed. Heats above 40°C may slowly break down the polymer. This cuts thickness over time. UV light can break down the cellulose spine. This also drops thickness. For best stability, store HPMC in sealed boxes in cool, dry spots away from direct sun. Well-stored HPMC can keep its thickness specs for 3-5 years.
Q5: What are the most common troubleshooting issues related to incorrect HPMC viscosity selection?
Common problems from wrong thickness picking are: (1) Poor water holding in mortars causing fast drying and weak bonds—often from picking too low thickness; (2) Too much thickening making products hard to mix or use—often from too high thickness; (3) Uneven drug release in pills—often from batch-to-batch thickness change; (4) Settling or splitting in liquid mixes—often from too little thickness; and (5) Long melting time during making—often from picking too high thickness without changing the steps. Most problems can be fixed by changing the thickness grade or changing the amount.