Selecting the correct Hydroxypropyl Methylcellulose (HPMC) grade is a critical decision for manufacturers across diverse industries. An incorrect choice can lead to significant production inefficiencies, compromised product quality, and ultimately, financial losses. You face challenges like inconsistent viscosity, poor water retention, or inadequate binding properties, which directly impact your final product’s performance and market acceptance. This is why understanding HPMC grades is so important. This article will guide you through the complexities of HPMC, detailing its properties, various grades, and optimal applications in pharmaceuticals, construction, and personal care. You will also learn how to troubleshoot common issues and make informed decisions for your specific project requirements.
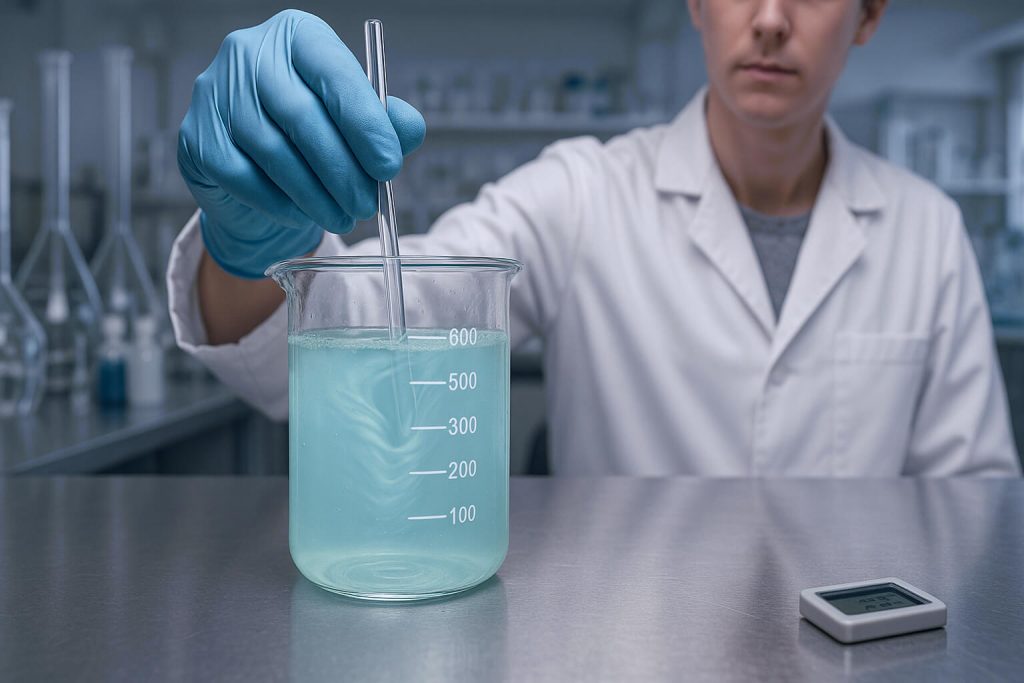
1. What is HPMC and why does it matter for your projects?
HPMC, or Hydroxypropyl Methylcellulose, is a versatile polymer derived from cellulose. It is a non-ionic, water-soluble ether of cellulose. This compound finds use in many industries. Its unique chemical structure allows it to perform several key functions. These functions include thickening, binding, film-forming, and water retention. Understanding these properties is key to successful application.
Property | Description | Typical Application |
---|---|---|
Thickening | Increases viscosity of solutions. | Paints, detergents, food products |
Binding | Holds components together. | Tablets, construction materials |
Film-forming | Creates a protective or functional film. | Coatings, personal care products |
Water Retention | Prevents water loss from formulations. | Mortars, baked goods |
Thermal Gelation | Forms a gel upon heating, reverts to liquid upon cooling. | Controlled release drugs, food gels |
Its broad application across pharmaceuticals, construction, food, and personal care highlights its importance. In pharmaceuticals, HPMC acts as a binder in tablets and a release modifier. In construction, it improves workability and adhesion of mortars. Food products use it for texture and stability. Personal care items benefit from its film-forming and thickening abilities. HPMC offers many benefits. It improves product performance and stability. It also extends shelf life. This makes it a valuable ingredient in many formulations.
2. How do different HPMC grades impact performance?
HPMC comes in various grades, each designed for specific performance characteristics. These differences stem from variations in molecular weight, degree of substitution, and particle size. Understanding these distinctions helps you select the right grade. This selection directly affects your product’s final performance.
Viscosity is a primary differentiator among HPMC grades. It dictates the thickening power of the HPMC. High-viscosity grades create thick solutions. Low-viscosity grades result in thinner solutions. This property is crucial for flow and application. For example, a high-viscosity HPMC is suitable for paints. A low-viscosity grade works well in eye drops. The substitution types, specifically methoxyl and hydroxypropoxyl content, also play a role. These affect solubility and thermal gelation. Higher methoxyl content often means lower gelation temperature. Higher hydroxypropoxyl content improves water solubility. Particle size influences dissolution rate. Finer particles dissolve faster. Coarser particles disperse better. This impacts mixing and processing. Gelation temperature is another key factor. It is the temperature at which an HPMC solution forms a gel. This property is vital for applications requiring heat stability. Purity and regulatory compliance are also critical. These ensure the HPMC meets industry standards. They also confirm it is safe for its intended use. This is especially true for pharmaceutical and food applications.
HPMC Property | Impact on Performance | Considerations |
---|---|---|
Viscosity Range | Controls thickening power and flow. | Application method, desired consistency |
Substitution Type | Affects solubility, thermal gelation, and film properties. | Water solubility, heat stability |
Particle Size | Influences dissolution rate and dispersion. | Mixing time, lump formation |
Gelation Temperature | Determines heat stability and gelling behavior. | Processing temperature, product stability |
Purity/Compliance | Ensures safety and meets industry standards. | Regulatory requirements, end-product safety |
Different HPMC grades offer distinct advantages. For instance, a high-viscosity HPMC with specific substitution levels might be ideal for a controlled-release pharmaceutical tablet. Conversely, a low-viscosity HPMC with different substitution could be perfect for a clear personal care gel. The choice depends on your specific needs. It also depends on the desired outcome. Consider all these factors. This ensures optimal product performance. It also helps meet regulatory demands.
3. Which HPMC grade suits pharmaceutical applications?
In the pharmaceutical industry, HPMC is a widely used excipient. Its versatility makes it suitable for various drug delivery systems. The choice of HPMC grade depends on the specific application. This choice impacts drug release and stability.
For solid dosage forms like tablets and capsules, HPMC acts as a binder. It provides mechanical strength. It also helps with disintegration. Different HPMC grades offer varying binding strengths. This affects tablet hardness. It also influences friability. HPMC is also crucial for controlled release formulations. It forms a gel layer around the tablet. This layer controls the drug release rate. High-viscosity HPMC is often preferred for extended-release. Low-viscosity HPMC might be used for immediate release. In liquid pharmaceuticals and suspensions, HPMC functions as a suspending agent. It prevents particle settling. It also improves consistency. This ensures uniform dosing. Regulatory standards and pharmacopoeial requirements are strict. HPMC used in pharmaceuticals must meet these. This includes standards like USP, EP, and JP. These standards ensure purity and quality. Case studies show HPMC’s role in drug delivery. For example, it is used in matrix tablets. It is also found in film coatings. These applications highlight its importance. They also show its adaptability.
Pharmaceutical Application | Recommended HPMC Properties | Example Grade Characteristics |
---|---|---|
Tablet Binding | Good compressibility, moderate viscosity | Low to medium viscosity, high purity |
Controlled Release | High viscosity, consistent gelation, low substitution | High molecular weight, specific methoxyl/hydroxypropoxyl ratio |
Suspension Stabilization | Medium to high viscosity, good suspending power | Medium viscosity, good water solubility |
Film Coating | Low viscosity, good film-forming, clear solutions | Low viscosity, excellent film properties |
Ophthalmic Solutions | Low viscosity, non-irritating, good clarity | Low viscosity, high purity, sterile |
Selecting the right HPMC grade for pharmaceutical use requires careful consideration. You must balance desired drug release profiles with processing needs. Regulatory compliance is also paramount. Working with a knowledgeable supplier helps ensure you choose the best grade. This guarantees product efficacy and safety.
4. What HPMC grades are optimal for construction materials?
In the construction industry, HPMC is a vital additive. It enhances the performance of various building materials. Its properties improve workability, adhesion, and durability. Choosing the right HPMC grade is crucial for construction project success.
HPMC is widely used in cement-based products. These include mortars, renders, and tile adhesives. It significantly impacts workability. It makes the mixture easier to spread. It also extends the open time. This allows more time for application. HPMC improves adhesion strength. It creates a stronger bond between materials. Water retention properties are also critical. HPMC prevents rapid water loss from the mixture. This ensures proper hydration of cement. It also reduces cracking. This leads to a more durable finish. HPMC influences sag resistance. It prevents vertical surfaces from slumping. This is important for thick applications. It also helps with crack prevention. This is due to improved hydration and reduced shrinkage. Specific HPMC grades are available for different construction needs. For example, some grades are designed for self-leveling compounds. Others are optimized for exterior insulation finishing systems (EIFS). These specialized grades ensure optimal performance. They also meet specific application demands.
Construction Application | Key HPMC Functionality | Desired HPMC Grade Characteristics |
---|---|---|
Tile Adhesives | Improved workability, extended open time, sag resistance | High water retention, medium to high viscosity |
Renders/Plasters | Enhanced adhesion, crack prevention, smooth finish | Good workability, moderate water retention |
Mortars | Better consistency, reduced segregation, increased strength | Medium viscosity, good water retention, air entrainment |
Self-Leveling Compounds | Flow control, reduced bleeding, improved surface finish | Low viscosity, good flow properties, rapid dissolution |
EIFS | Adhesion to insulation, flexibility, weather resistance | High water retention, good film-forming, high viscosity |
Selecting the optimal HPMC grade for construction materials involves considering several factors. You must account for the type of material, application method, and desired performance. The right HPMC grade can lead to significant improvements. It enhances material quality. It also boosts construction efficiency. This results in better, longer-lasting structures.
5. How does HPMC perform in personal care and cosmetic products?
In the personal care and cosmetic industry, HPMC is a valuable ingredient. It contributes to product stability, texture, and sensory appeal. Its diverse properties make it suitable for a wide range of formulations. This makes HPMC a versatile choice for many cosmetic applications.
HPMC serves as a thickener and stabilizer in creams and lotions. It provides a desirable consistency. It also prevents separation of ingredients. This ensures a smooth, uniform product. Its film-forming properties are beneficial in hair care and styling products. HPMC creates a light, flexible film on hair. This offers hold and protection. It also reduces frizz. In detergents and cleaning agents, HPMC acts as a rheology modifier. It controls flow and prevents settling of active ingredients. This ensures product effectiveness. Compatibility with other ingredients is crucial in personal care formulations. HPMC is generally compatible with a wide range of common cosmetic ingredients. This includes surfactants, emollients, and preservatives. Sensory attributes are also important. HPMC can improve the feel of a product on the skin or hair. It can provide a smooth, non-tacky sensation. This enhances the overall user experience. Consumer perception is influenced by these attributes. A pleasant texture and feel contribute to product acceptance. This makes HPMC a preferred choice for many formulators.
Personal Care Product | HPMC Function | Benefits |
---|---|---|
Creams and Lotions | Thickener, stabilizer | Smooth texture, improved spreadability, enhanced stability |
Shampoos and Conditioners | Thickener, foam enhancer | Rich lather, improved viscosity, better hair feel |
Hair Gels and Mousses | Film-former, rheology modifier | Strong hold, non-flaking, natural feel |
Liquid Soaps | Thickener, suspending agent | Consistent viscosity, prevents ingredient settling |
Sunscreens | Thickener, emulsion stabilizer | Even application, improved water resistance |
Selecting the appropriate HPMC grade for personal care products involves considering the desired texture, stability, and sensory profile. You must also account for compatibility with other ingredients. The right HPMC grade can significantly enhance product performance. It also improves consumer satisfaction. This helps create high-quality, appealing personal care items.
6. What factors guide HPMC grade selection?
Choosing the correct HPMC grade is a systematic process. It involves evaluating several key factors. These factors ensure the selected grade meets your specific application needs. Careful consideration of these elements prevents costly mistakes.
First, consider your project-specific requirements. What rheology do you need? What setting time is ideal? What stability is necessary? For example, a fast-setting mortar needs a different HPMC than a slow-release pharmaceutical tablet. Compatibility with other raw materials is also vital. HPMC must work synergistically with all components in your formulation. Incompatibility can lead to undesirable reactions. It can also cause product failure. Processing conditions and equipment also play a role. Some HPMC grades disperse better in cold water. Others require hot water. Your mixing equipment might also influence the choice. A high-shear mixer might handle different HPMC types than a low-shear one. A cost-benefit analysis of different grades is also important. While a premium grade might offer superior performance, a more economical option might suffice. You must balance performance with cost. Supplier support and technical assistance are invaluable. A good supplier offers technical data. They also provide application guidance. They can help troubleshoot issues. This support ensures you make an informed decision. It also helps optimize your formulation.
Factor | Description | Example Consideration |
---|---|---|
Project Requirements | Desired rheology, setting time, stability, final product properties | Viscosity, gelation temperature, water retention |
Compatibility | Interaction with other raw materials in the formulation | pH sensitivity, ionic strength, presence of other polymers |
Processing Conditions | Temperature, mixing equipment, order of addition | Dissolution rate, dispersion characteristics |
Cost-Benefit Analysis | Balancing performance with economic viability | Price per kg, dosage required, overall formulation cost |
Supplier Support | Technical data, application guidance, troubleshooting | Technical data sheets, formulation support, sample availability |
By systematically evaluating these factors, you can confidently select the optimal HPMC grade. This approach minimizes risks. It also maximizes the performance of your product. It ensures your project meets its technical and economic goals.
7. How can you troubleshoot common HPMC application issues?
Even with careful selection, HPMC application can sometimes present challenges. Knowing how to troubleshoot common issues saves time and resources. Effective problem-solving ensures consistent product quality.
One common issue is poor dissolution or lump formation. This often happens when HPMC is added too quickly to water. It can also occur if the water is too cold. To address this, try pre-dispersing HPMC in a non-solvent. This could be glycerin or propylene glycol. Then, add this slurry to water. Alternatively, use hot water for initial dispersion. Then, cool it to allow full dissolution. Challenges with viscosity control are also frequent. If viscosity is too low, you might need a higher HPMC concentration. Or, you might need a higher viscosity grade. If it is too high, reduce the concentration. Or, switch to a lower viscosity grade. Ensure proper mixing time. This allows HPMC to fully hydrate. Problems related to film integrity or adhesion can arise. This is common in coatings. It can be due to insufficient HPMC concentration. It can also be due to improper drying conditions. Adjust HPMC levels. Optimize drying temperatures and times. Tips for optimizing HPMC dispersion include using a high-shear mixer. Also, add HPMC slowly with continuous agitation. This prevents clumping. When all attempts fail, seek expert consultation. Suppliers often have technical support teams. They can provide valuable insights. They can also offer solutions based on their experience. This helps you overcome complex issues.
Issue | Common Causes | Troubleshooting Steps |
---|---|---|
Poor Dissolution/Lumps | Rapid addition, insufficient agitation, cold water | Pre-disperse in non-solvent, add slowly, use hot water then cool |
Inconsistent Viscosity | Incorrect HPMC concentration, incomplete hydration, temperature variations | Adjust concentration, ensure full hydration, control temperature |
Poor Film Integrity/Adhesion | Insufficient HPMC, improper drying, incompatible ingredients | Increase HPMC, optimize drying, check ingredient compatibility |
Foaming | High agitation, certain HPMC grades | Reduce agitation, use anti-foaming agents, select low-foaming HPMC |
Gelation Issues | Incorrect temperature, wrong HPMC grade | Verify temperature, choose HPMC with appropriate gelation temp |
By understanding these common issues and their solutions, you can maintain efficient production. You can also ensure high-quality products. Proactive troubleshooting minimizes downtime. It also reduces material waste. This leads to better overall operational efficiency.
Conclusion
Selecting the right HPMC grade is a strategic decision. It directly impacts product performance and manufacturing efficiency. We have explored HPMC’s fundamental properties. We also examined its diverse applications across pharmaceuticals, construction, and personal care. Understanding the nuances of viscosity, substitution, and particle size helps you make informed choices. By carefully matching HPMC grades to your specific project needs, you can achieve superior product quality. You can also optimize production processes. This leads to reduced waste and improved cost-effectiveness. Morton offers expert guidance and a comprehensive range of HPMC solutions. Partner with Morton to refine your formulations. Access our technical support and discover how our HPMC grades can elevate your product standards. We are committed to helping you achieve your manufacturing goals.
FAQ
Q1: What is the primary function of HPMC in most applications?
HPMC primarily functions as a thickener, binder, and film-former, enhancing consistency, adhesion, and stability across various products.
Q2: Can HPMC be used in both water-based and solvent-based systems?
HPMC is primarily water-soluble, making it ideal for water-based systems. Modified HPMC grades can offer improved compatibility with certain organic solvents.
Q3: How does HPMC viscosity relate to its application?
Higher viscosity HPMC grades provide greater thickening and water retention, while lower viscosity grades are suitable for applications requiring less thickening or faster dissolution.
Q4: Is HPMC safe for use in food and pharmaceutical products?
Yes, specific grades of HPMC are approved for use in food and pharmaceutical products, adhering to strict regulatory standards for purity and safety.
Q5: What is the significance of gelation temperature in HPMC selection?
Gelation temperature indicates the point at which an HPMC solution forms a gel upon heating. This property is crucial for applications where thermal stability or controlled release is desired.