Hydromellose, or HPMC, is a versatile polymer used across many industries. Choosing the correct grade, such as HPMC K4M or HPMC 2208, is critical for product performance. Incorrect selection can lead to manufacturing inefficiencies, compromised product quality, and significant financial losses. This often results in costly re-formulations and delayed market entry, impacting your bottom line and market reputation. Understanding the specific properties and applications of each HPMC type helps you avoid these pitfalls, ensuring optimal product development and manufacturing efficiency. This article will guide you through the distinctions between HPMC K4M and HPMC 2208, helping you make informed decisions for your applications by examining their composition, properties, and optimal uses.
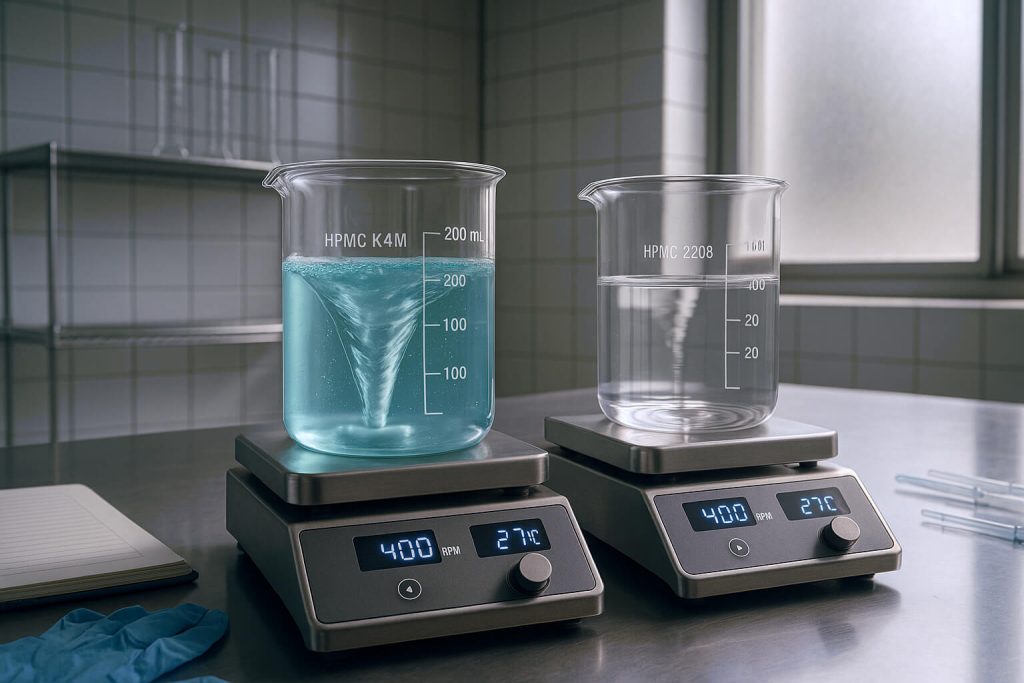
1. What is HPMC and how does it function?
HPMC, or hydroxypropyl methylcellulose, is a cellulose ether. It is derived from cellulose, a natural polymer found in plant cell walls. The chemical modification process involves treating cellulose with methyl chloride and propylene oxide. This creates a non-ionic, water-soluble polymer. HPMC is widely used due to its unique properties. These include thickening, film-forming, water retention, and binding capabilities. Here’s why it matters: These properties make HPMC valuable in many applications. It functions as a rheology modifier, a binder, a film former, and a water retention agent. Its versatility makes it a staple in diverse sectors. It is used in pharmaceuticals, construction, and food products. In pharmaceuticals, HPMC acts as a binder in tablets. It also controls drug release in sustained-release formulations. In construction, it improves workability and adhesion of mortars. In food, it serves as a thickener and stabilizer. Each application benefits from HPMC’s specific functional attributes.
Property | Description |
---|---|
Thickening | Increases viscosity of solutions |
Film-forming | Creates clear, flexible films |
Water Retention | Prevents water loss in formulations |
Binding | Holds components together in solid forms |
Emulsifying | Stabilizes immiscible liquids |
2. How do HPMC K4M and HPMC 2208 differ in composition?
The primary distinction between HPMC K4M and HPMC 2208 lies in their substitution patterns. HPMC is synthesized by substituting hydroxyl groups on the cellulose backbone. These are replaced with methoxy and hydroxypropoxy groups. The degree of substitution (DS) and molar substitution (MS) define the specific HPMC grade. HPMC K4M typically has a higher degree of methoxy substitution. HPMC 2208 has a different balance of these groups. This compositional difference impacts their physical and chemical behaviors. Let me explain: The ratio of methoxy to hydroxypropoxy groups influences solubility. It also affects gelation temperature and viscosity. These variations are critical for specific applications. For example, a higher methoxy content generally leads to lower gelation temperatures. This affects how the HPMC behaves under heat. The substitution type also impacts surface activity. This is important for film formation and emulsification. Understanding these subtle compositional differences is key. It helps in selecting the right HPMC grade for your product. Different substitution patterns yield different performance characteristics. This makes each grade suitable for distinct uses.
Feature | HPMC K4M (Typical) | HPMC 2208 (Typical) |
---|---|---|
Methoxy Content | Higher | Lower |
Hydroxypropoxy Content | Lower | Higher |
Substitution Type | Balanced for high viscosity | Balanced for broad utility |
3. What are the distinct physical properties of HPMC K4M and HPMC 2208?
HPMC K4M and HPMC 2208 exhibit distinct physical properties. These properties dictate their suitability for various applications. Viscosity is a key differentiator. HPMC K4M is known for its high viscosity. It forms highly viscous solutions even at low concentrations. This makes it ideal for applications requiring significant thickening. HPMC 2208, while also a thickener, generally offers a broader range of viscosities. Its viscosity can be tailored for diverse needs. Gelation temperature is another critical property. This is the temperature at which the HPMC solution forms a gel upon heating. HPMC K4M typically has a lower gelation temperature. HPMC 2208 often has a higher one. This impacts thermal stability during processing. Solubility and dissolution rates also vary. HPMC K4M may dissolve more slowly due to its higher molecular weight. HPMC 2208 might dissolve more readily. Particle size and morphology also play a role. These factors influence dispersion and hydration. But here’s the thing: These physical differences directly translate to performance. They determine how each HPMC grade functions in a final product. For instance, a higher viscosity HPMC K4M is excellent for controlled-release tablets. A more soluble HPMC 2208 might be better for quick-dissolving formulations. Careful consideration of these properties is vital for product success.
Property | HPMC K4M Characteristics | HPMC 2208 Characteristics |
---|---|---|
Viscosity Range | High (e.g., 4,000 mPa·s) | Medium to High (e.g., 2,200 mPa·s) |
Gelation Temperature | Lower (e.g., 60-65°C) | Higher (e.g., 70-75°C) |
Dissolution Rate | Slower, controlled hydration | Faster, more rapid hydration |
Film Strength | High, durable films | Good, flexible films |
4. Where is HPMC K4M best applied in industrial settings?
HPMC K4M finds its niche in industrial applications demanding high viscosity and controlled release. In pharmaceuticals, it is a preferred choice for sustained-release matrix tablets. Its high viscosity helps form a robust gel layer. This layer controls the diffusion of the drug. This ensures a prolonged therapeutic effect. For example, in extended-release pain medications, HPMC K4M provides the necessary matrix. This allows for a steady drug release over many hours. In the construction industry, HPMC K4M is used in tile adhesives and renders. It improves water retention and workability. This prevents premature drying of cementitious materials. It also enhances adhesion strength. This is crucial for durable construction. This is important because: Its high water retention capacity ensures proper cement hydration. This leads to stronger, more reliable bonds. Other industrial uses include paints and coatings. Here, it acts as a thickener and rheology modifier. It prevents sagging and improves application properties. It is used in formulations where consistent performance is paramount. This includes specialized industrial glues and thickeners.
Application Area | Specific Use Case | Benefit of HPMC K4M |
---|---|---|
Pharmaceuticals | Sustained-release tablets | Controlled drug diffusion, prolonged effect |
Construction | Tile adhesives, renders | Improved water retention, enhanced adhesion |
Paints & Coatings | Thickeners, rheology modifiers | Prevents sagging, better application |
Industrial Adhesives | High-strength binders | Strong, durable bonding |
5. What are the optimal applications for HPMC 2208?
HPMC 2208 is highly versatile. It finds optimal applications in diverse sectors. These include personal care, food, and specific pharmaceutical uses. In personal care products, HPMC 2208 is common in shampoos, lotions, and creams. It functions as a thickener, stabilizer, and emulsifier. Its ability to create smooth textures and stable emulsions is valued. For example, in a moisturizing lotion, HPMC 2208 provides the desired consistency. It also helps distribute active ingredients evenly. In the food industry, it acts as a thickener, binder, and stabilizer. It is used in sauces, dressings, and baked goods. It improves texture and prevents syneresis. This ensures product quality over time. Now, you might be wondering: How does it perform in pharmaceuticals? HPMC 2208 is used in pharmaceutical applications where specific dissolution profiles are needed. It can be used in immediate-release tablets as a binder. It also works in certain film coatings. Its properties allow for faster disintegration compared to higher viscosity grades. This makes it suitable for formulations where rapid drug release is desired. Its balanced properties make it a go-to choice for many consumer-facing products. It offers both functional benefits and ease of processing.
Application Area | Specific Use Case | Benefit of HPMC 2208 |
---|---|---|
Personal Care | Shampoos, lotions, creams | Thickening, stabilization, smooth texture |
Food Industry | Sauces, dressings, baked goods | Texture improvement, anti-syneresis |
Pharmaceuticals | Immediate-release tablets, coatings | Binder, controlled disintegration |
Cosmetics | Gels, mascaras | Viscosity control, film formation |
6. How do processing considerations impact HPMC selection?
Selecting the right HPMC grade involves more than just end-product performance. Processing considerations play a significant role. The ease of mixing and dispersion is crucial. Some HPMC grades may disperse more readily in water. Others might require specific mixing techniques to avoid lumps. For instance, HPMC K4M, with its higher viscosity, might need slower addition to water. This ensures proper hydration without clumping. HPMC 2208 might be more forgiving in terms of mixing. Compatibility with other excipients or additives is also vital. HPMC must not react adversely with other components in the formulation. This could compromise product stability or efficacy. For example, certain pH levels or ionic strengths can affect HPMC’s performance. Want to know the secret? Pre-testing compatibility saves time and resources. It prevents costly production issues. Stability under various processing conditions is another factor. This includes temperature, shear, and pH changes during manufacturing. Some HPMC grades are more robust under high shear. Others might degrade. Understanding these processing nuances helps optimize manufacturing. It ensures consistent product quality. Choosing an HPMC that integrates smoothly into your existing process is key. It streamlines production and reduces waste.
7. What regulatory and quality standards apply to HPMC K4M and HPMC 2208?
Regulatory compliance and quality standards are paramount for HPMC. Especially in pharmaceutical and food applications. Both HPMC K4M and HPMC 2208 must meet stringent pharmacopoeial requirements. These include standards set by the United States Pharmacopeia (USP). They also include the European Pharmacopoeia (EP) and Japanese Pharmacopoeia (JP). These standards define purity, assay, and physical properties. They ensure the HPMC is safe and effective for its intended use. For food applications, HPMC must comply with food-grade certifications. These are issued by bodies like the FDA or EFSA. These certifications confirm the HPMC is safe for consumption. Quality control parameters are also critical. These include tests for viscosity, moisture content, and heavy metals. Microbial limits are also checked. The bottom line? Adherence to these standards ensures product safety. It also guarantees consistent performance. Suppliers must provide certificates of analysis. These documents confirm that the HPMC meets all specified quality and regulatory criteria. Choosing a supplier with a strong track record of compliance is essential. It mitigates risks and ensures product integrity. This is particularly true for sensitive applications like pharmaceuticals.
8. How can you choose the right HPMC for your specific needs?
Choosing the right HPMC grade requires a systematic approach. First, clearly define your application requirements. Consider the desired viscosity, dissolution profile, and thermal stability. For example, if you need a sustained-release agent, HPMC K4M might be suitable. If you need a quick-dissolving binder, HPMC 2208 could be better. Next, conduct a thorough cost-benefit analysis. Higher-grade HPMC might offer superior performance. However, it may also come at a higher cost. Balance performance needs with budget constraints. What does this mean for you? Sometimes, a slightly less expensive grade can still meet your requirements. Finally, leverage the technical support offered by suppliers. Reputable HPMC manufacturers provide detailed data sheets. They also offer application guidance. Their expertise can help you fine-tune your selection. They can also assist with formulation challenges. Pilot trials and small-scale testing are also recommended. This confirms the chosen HPMC performs as expected in your specific formulation. This comprehensive approach minimizes risks. It ensures you select the most appropriate HPMC grade for your product success.
Conclusion
Selecting the correct HPMC grade, whether HPMC K4M or HPMC 2208, is a critical decision impacting product quality and manufacturing efficiency. We have explored the compositional differences, distinct physical properties, and optimal applications for each. Understanding these nuances helps you avoid common pitfalls and optimize your formulations. From controlled-release pharmaceuticals with HPMC K4M to personal care products using HPMC 2208, each grade offers unique advantages. Making an informed choice ensures your product performs as intended and meets regulatory standards. To discuss your specific HPMC needs and find the perfect solution for your application, contact Morton today. We provide expert guidance and high-quality HPMC products tailored to your requirements.
FAQ
Q1: What is the primary difference between HPMC K4M and HPMC 2208?
HPMC K4M typically has a higher viscosity and is often used for sustained-release applications, while HPMC 2208 offers a broader viscosity range and is suitable for diverse uses including personal care and immediate-release formulations.
Q2: Can HPMC K4M and HPMC 2208 be used interchangeably in formulations?
No, they cannot be used interchangeably without careful consideration. Their distinct compositional and physical properties mean they perform differently in formulations, impacting factors like dissolution rate, viscosity, and gelation temperature.
Q3: How does viscosity affect the performance of HPMC in an application?
Viscosity directly impacts thickening, binding, and controlled-release properties. Higher viscosity HPMC grades, like K4M, create thicker solutions and more robust matrices for sustained drug release, while lower viscosity grades are used for different flow characteristics.
Q4: What regulatory considerations are important when selecting HPMC?
Regulatory considerations include compliance with pharmacopoeial standards (USP, EP, JP) for pharmaceutical use and food-grade certifications for food applications. Quality control parameters like purity, moisture content, and heavy metals are also crucial.
Q5: Where can I find reliable technical data for HPMC grades?
Reliable technical data for HPMC grades can be obtained directly from reputable manufacturers and suppliers. They typically provide detailed product specifications, certificates of analysis, and application guides to assist with selection and formulation.