Tile adhesive performance directly impacts construction project success. Poor adhesion leads to costly failures and rework, causing significant delays and budget overruns for B2B buyers. Here’s why it matters: substandard materials compromise structural integrity and client satisfaction. This article explains how Hydroxypropyl Methylcellulose (HPMC) provides a reliable solution, enhancing tile adhesive properties for superior, lasting results. We will cover HPMC’s role, benefits, application, and future trends in tile adhesive technology.
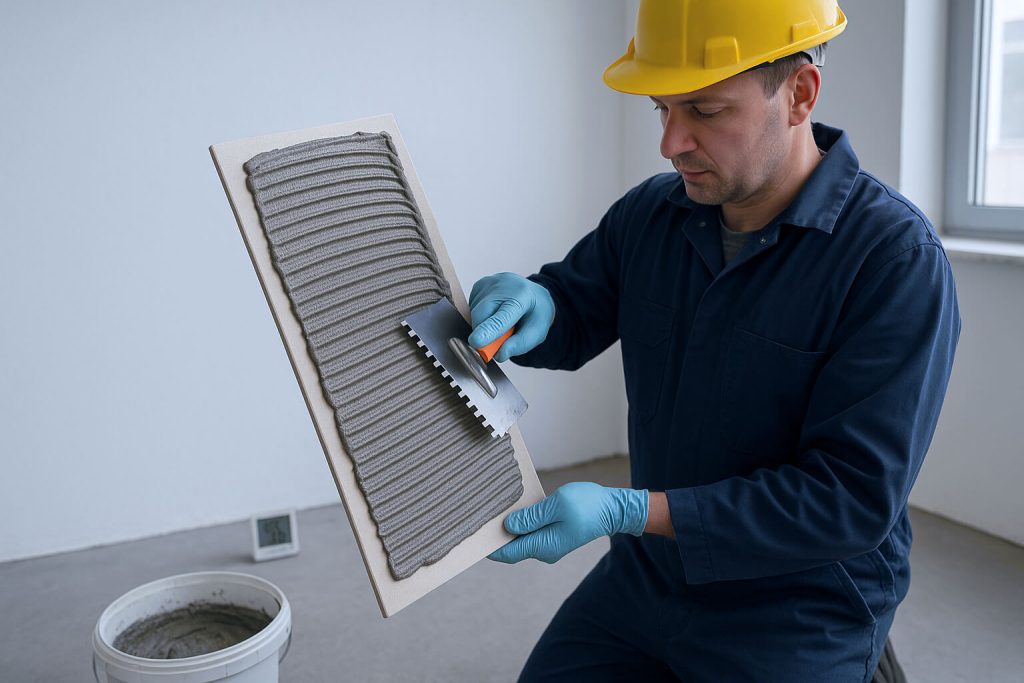
1. What is Hydroxypropyl Methylcellulose (HPMC)?
Hydroxypropyl Methylcellulose, or HPMC, is a versatile polymer derived from cellulose. It is a non-ionic cellulose ether, produced through a chemical process that modifies natural cellulose. This modification involves reacting cellulose with propylene oxide and methyl chloride. The resulting compound is a white, odorless powder. It dissolves in cold water to form a clear or slightly hazy solution. This solution exhibits pseudoplastic behavior. Let me explain: its viscosity decreases under shear stress, making it ideal for various applications.
HPMC’s chemical structure provides its unique properties. It has both hydrophilic (water-loving) and hydrophobic (water-fearing) groups. This dual nature allows it to interact with both water and organic compounds. These interactions are crucial for its function in construction materials. HPMC acts as a binder, thickener, and water retention agent. It also provides film-forming capabilities. These attributes make it valuable in many industries. These include pharmaceuticals, food, cosmetics, and construction.
In construction, HPMC is a key additive. It improves the performance of cement-based products. These products include tile adhesives, renders, and self-leveling compounds. Its primary role is to control water migration. It also enhances workability and adhesion. The molecular weight and degree of substitution influence its properties. Different grades of HPMC are available. Each grade offers specific performance characteristics. These are tailored for different applications.
Property | Description |
---|---|
Appearance | White to off-white powder |
Solubility | Soluble in cold water, insoluble in hot water |
Viscosity | Varies by grade, forms viscous solutions |
pH Stability | Stable over a wide pH range |
Water Retention | High, prevents rapid water loss |
Film Formation | Forms clear, flexible films |
2. How Does HPMC Improve Tile Adhesive Performance?
HPMC significantly enhances the performance of tile adhesives. Its primary function is water retention. This property is vital for cement hydration. When HPMC is present, it slows down water evaporation. This allows the cement to fully hydrate. Proper hydration leads to stronger bonds. It also extends the open time of the adhesive. This gives installers more time to adjust tiles. This is important because: it reduces errors and improves installation quality.
Another key role of HPMC is thickening. It increases the viscosity of the adhesive mixture. This prevents sag, especially with heavy tiles. It also improves the adhesive’s rheology. This means it flows smoothly during application. Yet, it remains stable once applied. This balance is critical for easy spreading. It also ensures proper coverage. The adhesive maintains its shape. This prevents tiles from slipping.
HPMC also improves the bond strength. It creates a more uniform and dense adhesive layer. This leads to better contact with the tile and substrate. The improved water retention ensures complete cement hydration. This further strengthens the bond. Adhesion is also enhanced by HPMC’s film-forming ability. This creates a strong interface. This results in a durable and long-lasting tile installation.
Performance Aspect | HPMC Contribution |
---|---|
Water Retention | Extends open time, aids cement hydration |
Thickening | Prevents sag, improves spreadability |
Open Time | Allows more time for tile adjustment |
Adhesion | Enhances bond strength to tile and substrate |
Workability | Smoother application, easier spreading |
3. What are the Key Benefits of Using HPMC in Tile Adhesives?
Using HPMC in tile adhesives offers many benefits. It increases application efficiency. Installers can work faster. The extended open time means less rush. The improved workability makes spreading easier. This reduces physical strain. It also allows for more precise placement. This leads to quicker project completion. The bottom line? You save time and labor costs.
Another benefit is reduced material waste. HPMC’s sag resistance means less adhesive drips. Its improved spreadability ensures even coverage. This prevents over-application. Less waste means more efficient use of materials. This directly impacts project budgets. It also contributes to sustainability efforts. This is a win-win for B2B buyers.
HPMC also enhances the durability of tiled surfaces. The stronger bond prevents cracking. It resists delamination. This is especially true in areas with temperature changes. It also holds up well in high-traffic zones. This means fewer repairs over time. Durable installations reduce maintenance costs. They also extend the lifespan of the tiled area. This provides long-term value.
Consistency in performance is another advantage. HPMC ensures the adhesive performs reliably. This is true across different environmental conditions. It maintains its properties in varying humidity. It also works well in different temperatures. This predictability is vital for large projects. It ensures uniform quality. This reduces risks for contractors.
Benefit | Impact on Tile Adhesive Performance |
---|---|
Efficiency | Faster application, reduced labor |
Waste Reduction | Less material loss, cost savings |
Durability | Stronger bonds, fewer cracks, longer lifespan |
Consistency | Reliable performance in varied conditions |
Cost-Effectiveness | Lower long-term maintenance and repair costs |
4. What Types of Tile Adhesives Benefit Most from HPMC?
HPMC is highly beneficial for cement-based tile adhesives. These adhesives rely on water for cement hydration. HPMC’s water retention property is crucial here. It ensures the cement fully reacts. This leads to maximum strength development. It also extends the working time. This is important for large-scale tiling jobs. It allows for adjustments. Now, you might be wondering: how does it help with different types of cement?
For dispersion-based tile adhesives, HPMC also plays a role. These adhesives are pre-mixed. They do not rely on cement hydration. HPMC acts as a thickener and rheology modifier. It improves the consistency of the adhesive. This makes it easier to spread. It also prevents slumping. This is important for vertical applications. It ensures the adhesive stays in place.
Specific applications gain significant advantages from HPMC. For large format tiles, sag resistance is critical. HPMC provides this. It prevents heavy tiles from slipping. In wet areas like bathrooms, strong adhesion is vital. HPMC enhances this. It ensures a durable, water-resistant bond. For outdoor applications, freeze-thaw stability is important. HPMC contributes to this. It improves the adhesive’s resilience.
Adhesive Type | HPMC Role |
---|---|
Cement-Based | Water retention, extended open time, strength |
Dispersion-Based | Thickening, rheology control, sag resistance |
Large Format Tiles | Prevents sag, improves bond for heavy tiles |
Wet Areas | Enhances water resistance, strong adhesion |
Outdoor Use | Improves freeze-thaw stability, durability |
5. How Does HPMC Affect the Curing Process of Tile Adhesives?
HPMC significantly influences the curing process of tile adhesives. Its primary impact is on the hydration of cement. It slows down the rate at which water is absorbed by the cement particles. This allows for a more complete hydration reaction. A more complete reaction leads to a stronger, denser matrix. This results in higher compressive and tensile strengths. Want to know the secret? It’s all about controlled water release.
This controlled hydration also affects drying time. HPMC prevents premature drying of the adhesive surface. This is especially important in hot or dry conditions. If the surface dries too quickly, it can form a skin. This skin can hinder proper bonding. HPMC ensures the adhesive remains workable. It also allows for uniform drying throughout the layer. This prevents internal stresses.
The role of HPMC in preventing premature drying is critical. It creates a protective film around the cement particles. This film acts as a barrier. It reduces the rate of water evaporation. This ensures that enough water is available for the cement to react fully. This leads to optimal strength development. It also minimizes shrinkage cracks. This improves the overall durability of the installation.
Curing Aspect | HPMC Influence |
---|---|
Cement Hydration | Slows water absorption, promotes complete reaction |
Drying Time | Prevents premature surface drying |
Shrinkage Cracks | Minimizes formation due to controlled drying |
Strength | Leads to higher compressive and tensile strengths |
Workability | Maintains workability during curing |
6. What are the Different Grades of HPMC for Tile Adhesives?
HPMC is available in various grades. These grades differ primarily in viscosity. Viscosity refers to the thickness of the solution. High-viscosity HPMC provides greater thickening. It offers better sag resistance. This is suitable for heavy tiles. Low-viscosity HPMC is easier to mix. It allows for higher concentrations. This is useful for specific applications. Here’s the deal: choosing the right viscosity is key.
The degree of substitution also defines HPMC grades. This refers to the number of hydroxyl groups replaced. It affects solubility and gelation temperature. Different substitution patterns influence performance. They impact water retention and open time. This allows for fine-tuning adhesive properties. It ensures optimal performance for various climates.
Particle size is another differentiating factor. Finer particles dissolve faster. They provide quicker viscosity build-up. Coarser particles dissolve slower. They offer a more gradual thickening effect. The dissolution rate impacts mixing time. It also affects the initial workability. Choosing the right particle size is important. It ensures efficient production and application.
HPMC Grade Factor | Impact on Tile Adhesive |
---|---|
Viscosity | Thickening, sag resistance, workability |
Substitution Degree | Solubility, gelation, water retention, open time |
Particle Size | Dissolution rate, mixing time, initial viscosity |
Purity | Consistency, absence of impurities |
pH | Stability in different adhesive formulations |
7. How is HPMC Incorporated into Tile Adhesive Formulations?
Incorporating HPMC into tile adhesive formulations requires careful steps. It is typically added as a dry powder. It is mixed with other dry components first. These include cement, sand, and other additives. This ensures uniform dispersion. Proper mixing prevents lumps. It guarantees consistent performance. But here’s the thing: the order of addition matters.
Mixing procedures are crucial. Dry blending is the first step. All powders are thoroughly mixed. This creates a homogeneous blend. Then, water is added gradually. This initiates the hydration process. High-shear mixers are often used. They ensure complete dissolution of HPMC. This prevents fish-eyes or undissolved particles. Proper mixing ensures optimal rheology.
Recommended dosage varies. It depends on the desired properties. It also depends on the specific HPMC grade. Typical concentrations range from 0.2% to 0.5% by weight. Higher dosages increase viscosity. They also improve water retention. However, excessive amounts can reduce bond strength. They can also cause stickiness. Careful calibration is necessary. This ensures balanced performance.
Compatibility with other additives is important. Tile adhesives often contain other chemicals. These include redispersible polymer powders. They also include defoamers and accelerators. HPMC must be compatible with these. Incompatibility can lead to poor performance. It can cause undesirable reactions. Testing is essential. This confirms compatibility. It ensures a stable formulation.
Incorporation Step | Description |
---|---|
Dry Blending | Mix HPMC with other dry powders for uniformity |
Water Addition | Gradually add water to initiate hydration |
Mixing Equipment | Use high-shear mixers for complete dissolution |
Dosage | Typically 0.2% to 0.5% by weight, adjust as needed |
Compatibility | Test with other additives to prevent issues |
8. What Quality Control Measures Apply to HPMC in Tile Adhesives?
Quality control for HPMC in tile adhesives is critical. It ensures consistent product performance. Testing methods for HPMC properties are essential. These include viscosity measurements. They also include water retention tests. Gelation temperature is another key parameter. These tests confirm the HPMC meets specifications. They ensure it performs as expected. Let me explain: rigorous testing prevents costly failures.
Standards and certifications guide quality control. Manufacturers adhere to industry standards. These ensure product consistency. They also guarantee safety. Certifications from independent bodies provide assurance. They confirm product quality. They also verify environmental compliance. This builds trust with B2B buyers. It ensures reliable supply chains.
Ensuring consistent product quality is paramount. Batches of HPMC must be uniform. Variations can affect adhesive performance. Quality control involves raw material inspection. It includes in-process monitoring. Final product testing is also crucial. This comprehensive approach minimizes defects. It guarantees reliable results. This protects brand reputation.
QC Measure | Purpose |
---|---|
Viscosity Testing | Confirms thickening power and workability |
Water Retention | Verifies open time and cement hydration |
Gelation Temp. | Ensures stability under varying temperatures |
Particle Size | Checks dissolution rate and mixing properties |
Purity Analysis | Detects contaminants, ensures consistent quality |
9. What are the Environmental and Safety Considerations for HPMC?
HPMC is generally considered environmentally friendly. It is derived from cellulose. Cellulose is a natural, renewable resource. HPMC is non-toxic. It is also biodegradable. This means it breaks down naturally. It does not harm the environment. This makes it a sustainable choice. The best part? It aligns with green building initiatives.
Handling and storage guidelines are straightforward. HPMC is a stable powder. It should be stored in a dry place. It needs protection from moisture. Moisture can cause clumping. It can affect its performance. Proper ventilation is also recommended. This prevents dust inhalation. Safety data sheets provide detailed information. They guide safe handling practices.
Regulatory compliance is important. HPMC is widely accepted. It meets various international standards. These include food and pharmaceutical regulations. Its use in construction is also regulated. This ensures its safety. It also guarantees its effectiveness. Compliance provides peace of mind. It simplifies product development.
Aspect | HPMC Characteristic |
---|---|
Source | Natural, renewable cellulose |
Toxicity | Non-toxic |
Biodegradability | Biodegradable, environmentally friendly |
Storage | Dry, protected from moisture, ventilated |
Regulations | Complies with international standards |
10. What Future Trends Impact HPMC Use in Tile Adhesives?
Future trends strongly influence HPMC use in tile adhesives. Sustainable building practices are gaining momentum. There is a growing demand for eco-friendly materials. HPMC fits this trend perfectly. Its natural origin and biodegradability make it ideal. It supports green construction. This drives its continued adoption. Here’s why it matters: environmental impact is a key concern.
Innovations in adhesive technology also play a role. Manufacturers seek higher performance. They want adhesives with improved properties. These include faster curing times. They also want enhanced flexibility. HPMC research focuses on these areas. New HPMC grades are being developed. These meet evolving market needs. They push the boundaries of performance.
Growing demand for high-performance materials is another trend. Modern construction requires more durable solutions. It needs materials that withstand extreme conditions. HPMC contributes to this. It enhances the strength and longevity of tile adhesives. This makes it indispensable. It ensures long-term reliability. This trend will continue to fuel HPMC demand.
Future Trend | Impact on HPMC Use |
---|---|
Sustainability | Increased demand for eco-friendly HPMC |
Adhesive Innovation | Development of new HPMC grades for enhanced performance |
High-Performance | Growing need for HPMC to improve durability |
Digitalization | Smart manufacturing, data-driven HPMC optimization |
Urbanization | Increased construction, higher HPMC consumption |
Conclusion
HPMC is a vital component in modern tile adhesives. It significantly improves water retention, workability, and bond strength. These enhancements lead to more efficient installations and greater durability. By using HPMC, you ensure your tiling projects meet the highest standards. This reduces long-term maintenance costs and enhances client satisfaction. For superior tile adhesive solutions that deliver consistent, reliable results, contact Morton today. We provide expert guidance and high-quality HPMC products tailored to your specific needs.
FAQ
Q1: What is the primary function of HPMC in tile adhesives?
HPMC primarily functions as a water retention agent and thickener, improving the workability, open time, and bond strength of tile adhesives.
Q2: Can HPMC be used in all types of tile adhesives?
HPMC is widely used in cement-based and dispersion-based tile adhesives, but specific grades are chosen based on the adhesive type and desired performance.
Q3: How does HPMC contribute to the durability of tiled surfaces?
HPMC enhances durability by improving adhesion and flexibility, which helps prevent cracking and delamination over time, especially in varying temperature and humidity conditions.
Q4: Is HPMC environmentally safe?
Yes, HPMC is generally considered environmentally safe. It is derived from cellulose, a natural polymer, and is non-toxic and biodegradable.
Q5: What factors influence the choice of HPMC grade for a tile adhesive?
Key factors include the desired water retention, viscosity, open time, sag resistance, and the specific type of cement or polymer used in the adhesive formulation.